来源:中国冷链物流网(www.cclcn.com)
1. 目的
确保原材料、半成品、成品的进、出库作业规范化、标准化,维持物品在库储存期间的品质,确保出入库数据的准确、帐实相符。
2. 范围
适用于公司的原材料、半成品、成品的进仓、出仓、储存及帐务管理。
3. 输入
3.1 供应商送来之原材料、半成品、成品。
3.2 车间生产之半成品。
3.3 车间生产之成品。
4.输出
按照物料的进、销、存管理,维持储存品,出入库数据准确、帐实相符。
5.职责
5.1 仓储部负责原材料、半成品、成品的收、发工作。在库产品的防护、标识、管理、帐务登录以及消防安全。
5.2 品质部负责进仓产品的检验,库存产品出现质量异常时的品质判定以及相应处理方法的讨论。
6.过程描述
仓储管理的控制由下面流程图说明:
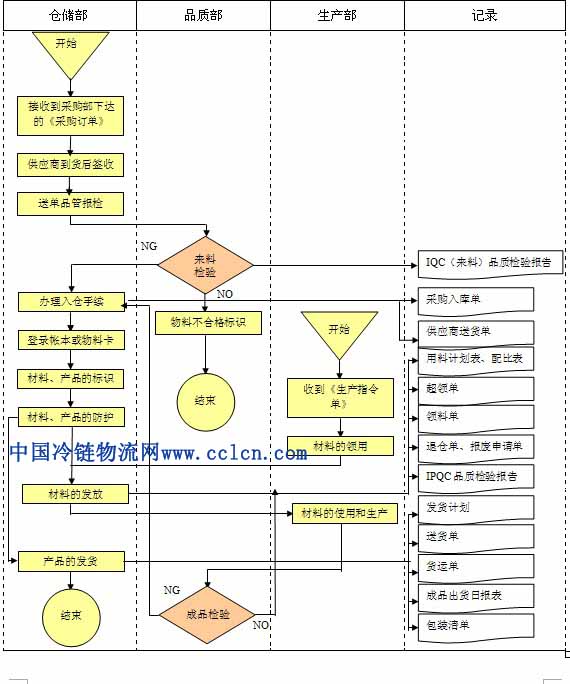
7.过程指引
7.1 收料作业
7.1.1 自制采购
7.1.1.1 仓库收料的依据是《采购订单》。
7.1.1.2 仓库根据采购提供的《来料计划知会表》,组织、安排人员准备验收供应商来料,凭采购订单、供应商送货单进行核对和点收数量,签单后送品管报检,等待品检出检验结果后,办理进仓手续,并于次日9:00前按《供应商送货单》来料情况反馈给物控部及采购部。当日应到而未到的物料于下午4:30
7.1.1.3 在收料过程中,因材料不合格由品质部填写《IQC(来料)品质检验报告》,对于现金采购的退货,依此开《退货单》办理退货手续。
7.1.2 客户提供产品作业
7.1.2.1 订单受理部在订单上注明客供产品的名称下达订单至PMC部,PMC部在标准用料表中注明客供产品的名称。
7.1.2.2 订单受理部需提供《客户供料通知书》下达至PMC部,PMC部下一步达仓储部。
7.1.2.3 仓储部根据《客户供料通知书》进行收货及报检,品质部依检验标准及《进料检验程序》执行。如在收货时发现产品多或少时,仓库应及时与订单受理部联系,并作出处理方式。
7.1.2.4 当客户供料储存、使用过程有变质、损坏或其它不适用的情形时,相关单位通知品质部进行检验,品质部填写《IQC(来料)检验报告》反馈仓储部及PMC部,由PMC部反应至订单受理部,订单受理部与客户联系决定处理方式。
7.2 仓储作业管理
7.2.1 仓库规划:仓库规划分为成品仓和原材料仓,原材料仓又分为转椅仓、五金仓、铝材仓、板材仓、布绒仓、外购配件仓、化学用品仓。
7.2.2 物品储存管理
7.2.2.1 原材料入库后,必须及时上架,并做好进仓日期标识。
7.2.2.2 库内产品摆放整齐,行列有序。
7.2.2.3 仓库整顿作业中,注意防止产品碰撞、倒塌现象,并要注意维护产品包装、产品标识。仓库应注意通风、防尘、防潮、防腐,防止产品被强光直接照射,并保持恰当的消防设备。
7.2.2.4 因地制宜,根据各种产品的特点实施先进先出,可以采用分区存放和出货,或者在每次进仓时将先入仓的材料移至外侧并先发货使用等方法。
7.2.2.5 注意油漆品、铝材喷涂料、MFC板材不遭受碰撞或挂花,严禁火种。
7.2.2.6 材料存放做到分类合理、摆放整齐、标识清晰。堆放过程中要做到平堆平放,防止板面划伤,发现板材表面有砂粒要随时扫净。
7.2.2.7真皮要放置在阴凉、干燥地方,防潮、防晒、防虫、防盗、防腐。
7.2.2.8 油漆、天那水、胶水等易燃物品,应单独房间存放,室内阴凉、通风良好。
7.2.2.9 仓库地面要保持清洁、干燥、灭火器安全有效。
7.3 帐务管理:
7.3.1 仓管员每日根据车间开出的《领料单》进行备料及发货;
7.3.2 收、发料后,应进行统计与帐务登记,并根据《安全库存量》及实物数书面知会PMC进行补仓。
7.4 物料库存稽查:
7.4.1 物料库存稽查:月盘点和年终盘点。每月进行帐面盘点,主要由仓库进行财务可派人会同仓管一道进行抽查。每季度和年终进行实物盘点,每季度及年终实物盘点由财务会同仓管共同进行。
7.4.2 在库存稽查中如发现产品超过保存期限,应及时将此信息反馈到品质部,由品质部派员对其进行质量确认并提出延长保存的期限,在得到品质部的肯定答复后,仓管员应尽快安排该产品的使用;如品质部判定该产品已经不适合使用,仓管员按照《不合格品控制过程》的要求进行。
7.5 领发料流程
7.5.1车间、仓库领发料的依据是《用料计划表》和《配比表》。
7.5.2车间领料单必须填写编码并于前一天下班前交到仓库备料。
7.5.3车间开领料单须按仓库分开填写。
7.5.4仓库与车间物料的交接必须当面点收,签名确认。
7.6 产品搬运
7.6.1 在产品的搬运过程中,人力搬运时,应考虑搬运质量负荷,省力化及安全化为原则进行,且注意物品轻拿轻放,放置地面时就平稳。
7.6.2 手推车、油压拖板车搬运时,应考虑产品的稳当性,高度不可超过1.5M,宽度不可宽于行走路线。物品应求平衡,宽大而重的物品置于下方,以求稳定搬运重心。
7.6.3 叉车搬运时,应考虑严禁超重,高度不可超过1.5M为原则,不得超快行驶,应顾及四周匀速行驶。避免紧急刹车,减少机械的损坏及载重物品的掉落,影响机械寿命。具体操作要求根据《叉车安全使用规定》。
7.6.4 产品搬运时,对易损易坏及外形,外观需进行保护的产品,用运输工具进行搬运时,需在运输工具与产品接触的地方用纸板和胶带包装保护,确保产品不受损坏。
7.7 出货作业程序
7.7.1 本厂送货
7.7.1.1 由客户服务部制订出每日《发货计划》至财务部和成品仓,经财务部审定并下达《送货单》至成品仓。然后客户服务部联系落实车辆。
7.7.1.2 成品仓收到《发货计划》及《送货单》后,即找出相应的《订购单》进行备货作业,理清各订单货品、配件,交付装车。
7.7.2客户提货
7.7.2.1成品仓收到《发货计划》及《送货单》后,即找出相应的《订购单》进行备货作业,理清各订单货品、配件,交付装车。
7.7.3 货物的交接
7.7.3.1 装车完毕,提货人员必须在相关发货单据上签名确认。
7.7.4 发货过程中,发现产品受损等异常情况,仓管员应即时通知相关品管员检查,并汇报主管处理,参照《不合格品控制过程》执行。
7.7.5 仓管员每日发货完毕,填写《成品出货日报表》,送客户服务部。
7.8客退作业程序
7.8.1成品仓接到客户服务部的《退/修通知单》(清单必须详细按实际包装情况填写,不能只笼统的写一套、一批;配件必须列出名称及数量),对客退品逐一清点数量,无误后签名确认并报品管检测判定处理办法。
7.8.2品质部接到客退品报检通知后应及时到场检测,根据实情作出处理意见。
7.8.3仓库根据品检意见,须车间返修后退回客户的与车间及时联系送车间返修,返修好后要及时通知客户服务部退回客户,出货程序同7.7;须返修入库的要送车间返修好后入库,对客退品建立专帐管理;配件良品退原材料仓并作好交接手续。
7.8.4客退成品如要报废的需报公司总经理审批后拆零成板退余料仓。
8.过程所需资源
8.1 仓管员:男性,年龄19-35岁,高中以上学历,一年以上仓库管理经验,对家具产品有所了解优先。
8.2 空间足够的库房,料架,包装容器,叉车或运输工具,消防器材和排气扇。
8.3 产品防护所需的恰当的保存环境。
9.相关文件
10.1 COP-720 客户相关过程
10.2 COP-742 采购过程
10.3 COP-821 服务提供过程
10.4 COP-830 不合格品控制过程
10.7 COP-852 纠正预防措施过程
10.相关记录
11.1 《用料计划表》
11.2 《进仓单》
11.3 《领料单》
11.4 《退仓单》
11.5 《报废申请单》
11.6 《超领单》
11.7 《客户供料通知书》
11.8 《进料检验报告》
11.9 《包装清单》
11.10 《发货计划》
11.11 《成品出货日报表》
11.12 《送货单》
11.13 《货运单》
|